
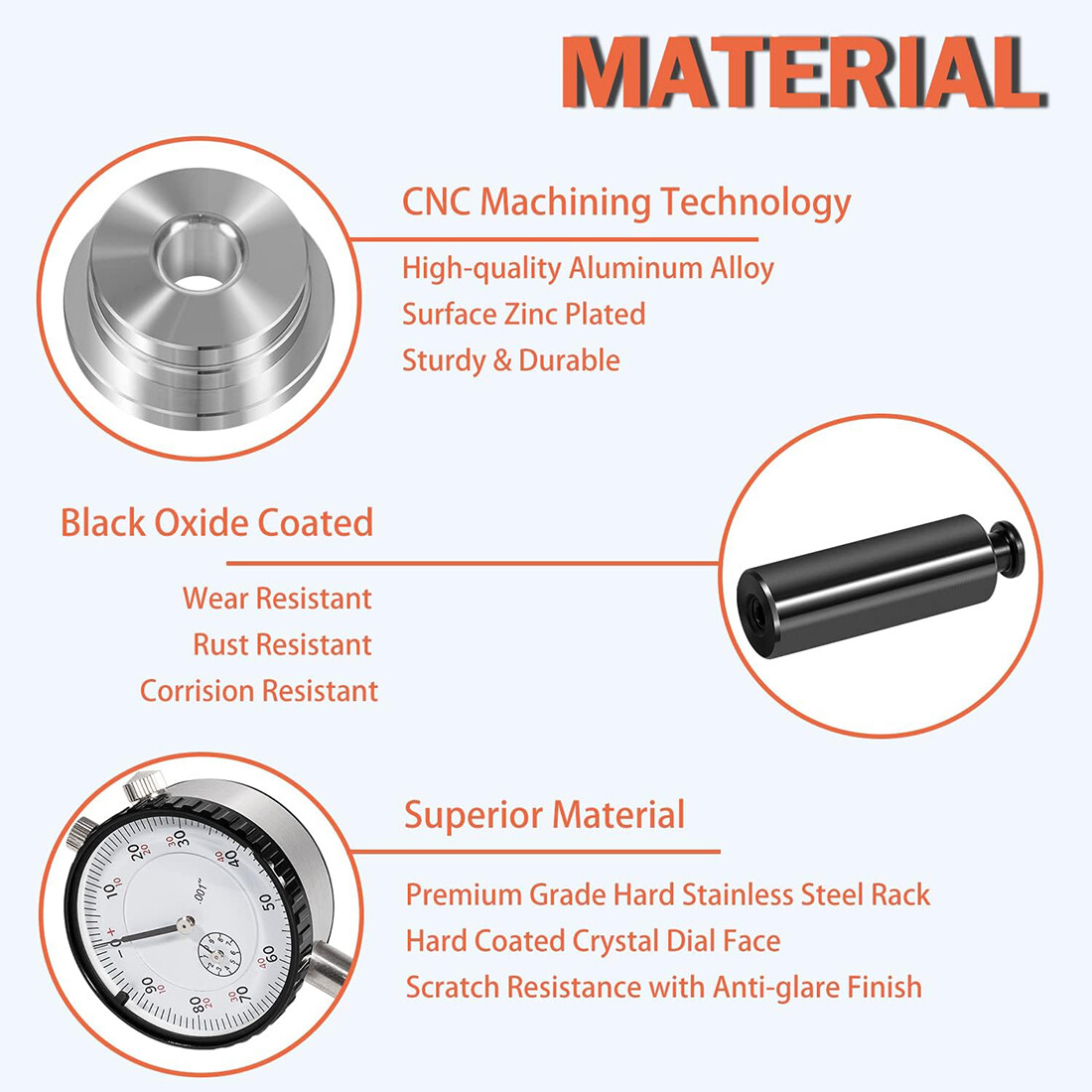



Application:
- Compatible with GM 10 and 12 bolt, for Ford 9”, 7.5″, 8.8″, 8”, for Dana 30, 35, 44, 50, 60, 70, 80, for Chrysler 10 and 12 bolt 8.75. (See description for fitment chart).

- This makes setting pinion depth more accurate and quickly.
- This tool is capable to measure many other Differentals you may just need a hub.
- Made of superior material (aluminum alloy, steel) which have an unparalleled lifespan with great durability.
- Designed to meet your specific needs.
- CSHAUCARLIF offer 100% new product, fast delivery and best customer service to every customer.
- If you have any problems, please feel free to contact us!

Deluxe Pinion Depth Gauge Checker Tool Kit Compatible With GM 10 12 Bolt, Ford 7.5” 8” 8.8” 9”, Chrysler 8 3/4”, Dana 30 35 44 50 60 70, and Most Differentials
Pinion Depth Checker
Set up your rearend the right way with a Pinion Depth Checker!
This is an indispensable tool whether installing one gearset a year or a dozen.
It’s easy to get a perfect tooth contact pattern with a pinion depth checker – far easier than the old trial and error methods. Installing the pinion at the correct depth extends gear life and reduces power-robbing friction.
Comes in a handy high-impact resistant carrying case.
The pinion depth checker kit is a very accurate method of setting pinion depth in a large number of automotive differentials. Alternative for T&D Machine Products 11001 Deluxe Pinion Depth Checker.
Instructions for the Deluxe Pinion Depth Checker Kit Introduction
Calibration
Note: Each of the three included calibration tubes is calibrated and sealed for each application.
1) lmportant: Before attempting calibration, carefully clean all parts. Any dirt can prevent a correct calibration.
2) Insert the Dial lndicator into the Cross Shaft with the Dial lndicator on the rounded side of the shaft and tip extending thru the flat area on the opposite side. Snug the setscrew making sure not to over-tighten.
3) Remove the Indicator Extension stored inside the appropriate Calibration Tube and screw the extension tip into the Dial lndicator until snug.
4) Hold the Cross Shaft and indicator assembly with the indicator tip pointed up. Slip the calibration tube over the tip and allow the tube to rest on the flat area on the cross shaft.
5)The thousandth (long arm) pointer should rotate clockwise slightly (about 0.020”) and be pointed approximately straight down, or in the 6 o’clock position. If the pointer does not point straight down, loosen the set screw in the cross shaft and raise or lower the indicator until the needle is pointed straight down with the calibration tube in place. Tighten the setscrew until snug (excessive tightening will lock the indicator shaft or permanently bend the housing) and make sure the pointer remains pointing straight down.
NOTE: Be sure that the short pointer (small dial) is in the “zero” position.
6) Loosen the indicator bezel lock screw and with the calibration tube in place, make the final adjustment by rotating the dial face until the zero aligns with the pointer. Tighten the indicator bezel lock screw. Your Pinion Depth Checker is now set and calibrated for a depth of exactly 3.375”(Or 1.900″ for the Ford 9” or 2.500” for the intermediate differentials). This is the CALIBRATED DEPTH.
MEASURING PINION DEPTH
1) Carefully remove any sharp edges or burrs from the carrier bearing housing and caps to avoid any inaccuracy or marring of the hubs.
2) Make note of the pinion depth inscribed on your pinion gear. If your pinion does not have a depth number on it, go to the “OEM GEAR APPLICATIONS” Section to find the pinion depth.
3) Place the pinion in the case with the appropriate bearings and shims.
4)Clean the appropriate Target Plate and the face of the pinion gear and then place the Target Plate on the face on the pinion.
5) Select the appropriate hubs and lightly oil the bores to prevent galling and carefully insert the Cross Shaft into the Hubs. Place this assembly in the case and tighten main cap bolts to 25 ft.-lbs. See picture for Hub Applications.
NOTE: The “A” diameter has a machined flat to clear the pinion support in Ford 9″ rear ends. Additional relief may be needed for individual applications. When using the “A” diameter in Dana 60s, the machined flat should be positioned at 90 degrees to the cap parting line.
6) Slide the Indicator and Cross Shaft as close as possible to pinion gear, minimizing any overhang of theTarget Plate. Be sure to retract the indicator plunger shaft just enough to clear the Target Plate to prevent bending the indicator.
7) Make sure the Indicator shaft end is seated on the target plate and note the reading on the dial. Multiply the small counter
umber by 0.100″ and add the thousandths pointer reading to get your INDICATOR READING. Subtract your lNDICATOR READING from the CALIBRATED DEPTH (3.375 for the long calibration tube, 2.500 for the intermediate, and 1.900 for the short) and you will have obtained your MEASURED PINION DEPTH.
Example: lf the reading on the indicator were 0.778″ (seven complete revolutions plus reading), subtracting from 3.375 would equal 2.597″. This is the MEASURED PINION DEPTH.
NOTE: To minimize error, rotate the pinion gear to at least four different positions and average the three most similar readings.
8) Compare the MEASURED PINION DEPTH to the Pinion Depth number inscribed on the
All major credit cards are accepted through secure payment processor PayPal.
International Buyers Please Note:
- Import duties, taxes and charges are not included in the item price or shipping charges. These charges are the buyer’s responsibility.
- Please check with your countries customs office to determine what these additional costs will be prior to bidding/buying.
- If you need to return, please double check to make sure the item does not work and contact our customer service representative, let us know the detailed problem and send us some photos for confirmation. Then get a unique address to return.
- Buyer is responsible for return shipping fee, including original freight, handling charges and the return freight when the returns is non-seller mistake (e.g. you purchased wrong model, wrong color or wrong size)
- We only accept return for original package, please make sure the item has not been used or installed.
- We reserve the right to refuse any return for any request that does not meet these requirements.







Reviews
There are no reviews yet.